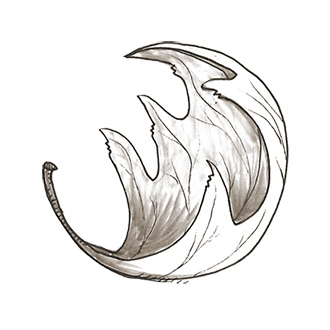
Related Questions
- How can we prevent walls from collapsing in earthquakes?
- What are the chances that a large asteroid will collide with Earth—and will we see it coming?
- How many solar panels do I need on my house to become energy independent?
- How can the average homeowner become energy-independent?
- Can nuclear waste be put to some positive use instead of just polluting the environment?
- Once air reaches the dew point, will the rate of condensation change if the temperature is lowered?
- Are nanoparticles harmful to the environment?
- How long does it take oil from an underwater spill to reach the surface?
- How can harmful substances be removed from waste water?
- Is corn the best source for ethanol?
What do we have to do to aluminum and plastic to recycle them?
Aluminum is pretty easy, but plastics can get a bit tricky…
By Sarah JensenOn Garbage Eve we tote our trash barrels to the curb and arrange them for the morning’s pickup. In the olden days (a decade or two ago, in most parts of the country) all of our household waste, including all the aluminum and plastic, was carted off to the landfill where it was left to slowly decompose. These days, however, many communities provide special bins for recyclable materials. On trash day, their contents are whisked away to processing centers where automatic spectroscopy systems separate glass from paper from plastic from aluminum — the first step in the recycling process.
“Aluminum is one of our most recycled materials and one of the easiest to reprocess,” says Allan Myerson, a professor in MIT’s chemical engineering department. “Recycling aluminum takes only 5 percent of the energy required to make new aluminum from bauxite ore, and it can be reused indefinitely without compromising its structure or function.” In fact, two-thirds of the aluminum ever manufactured is still being used in one form or another. In 2010, 58.1 percent of all aluminum cans were recycled, reflecting significant savings in manufacturing costs given the tens of billions of cans produced each year.
“Recycling aluminum simply involves melting the metal,” says Myerson. “Aluminum is relatively pure and doesn’t require a lot of secondary processing.” In the reclamation plant, aluminum items are shredded, chemically cleaned, and heated to about 750-800° C. Oxides and other minor impurities rise in the liquid aluminum and form dross, a solid easily skimmed from the surface. The molten aluminum is then poured into ingots that are sent to manufacturers for the production of rain gutters, computer components, boats, planes, and bicycle frames — and more soda cans.
“Recycling plastics is more complicated because there are several different kinds of plastics,” says Myerson. Each type requires different processing methods due to additives such as dyes and fillers that must be removed before it can be reused. To help with initial curbside sorting, the Society of the Plastics Industry created the resin identification code, a set of numbers and symbols stamped on plastic consumer goods indicating the type of plastic and its potential for recycling.
“The kind of plastic used in soda bottles is polyethylene terephthalate or PET,” explains Myerson. “It has a code of 1 and is one of the more recyclable plastics.” Shredded and cleaned, PET is melted or pelletized, then spun into thread for the manufacture of polyester fleece and carpet. High-density polyethylene (HDPE), used in milk and juice jugs, detergent bottles, and other sturdy containers, is coded 2 and finds new life as plastic lumber, tables, and benches. Its strength makes it the most useful and most often recycled plastic.
“The key with plastic recycling is that there must be both an environmental and an economic advantage,” says Myerson. “You don’t want to employ a recycling process that creates more pollution or consumes more energy than the problems it solves.” Polystyrene, for example — a plastic used for everything from packing peanuts to takeout containers to rigid foam insulation — is seldom recycled due to its low density. The energy required to compact it into a usable material is cost-prohibitive, and it’s more economical to haul it to the landfill, where it accounts for about 30 percent of the material there.
Continued research into the properties and chemical behavior of plastics will resolve such issues, suggests Myerson. “Hopefully, it will lead to better ways of both manufacturing and recycling plastics, and other materials as well.”
Thanks to Ivar from Odense, Denmark, for this question.
Posted: February 5, 2013