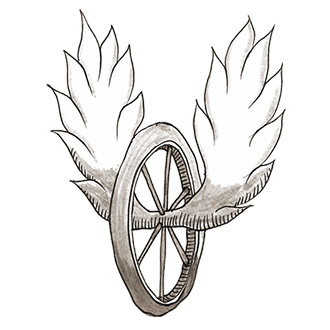
Related Questions
- Will cars ever be able to drive themselves?
- What is the relationship between the length of a boat and its maximum speed?
- Can robotic submarines collect specimens at any ocean depth?
- How does a jet engine work?
- Why hasn’t commercial air travel gotten any faster since the 1960s?
- How does an aircraft steer while taxiing on a runway?
- Can I start my car with a voice command?
- Is it possible to make solar-powered airplanes?
- Will public transportation ever replace the automobile?
- What are the future propulsion systems for interplanetary travel?
How do the blades of a jet engine start turning?
With a little push from the auxiliary power unit…
By Sarah JensenWhen a pilot pulls a commercial aircraft into an airport gate, he doesn’t just throw it into park and leave the engines idling. In fact, explains Max Brand, a master’s candidate working in the Gas Turbine Lab in MIT’s aeronautics and astronautics department, jet engines are switched off when an airplane is at the gate. However, as anyone who has walked on an airplane knows, it isn’t completely off. The lights are on and the plane is humming under your feet. You may even have noticed exhaust coming from the rear of the plane when you looked out the window in the gate area.
“The exhaust is from the auxiliary power unit,” Brand says. “The APU is like a mini jet engine, usually located in the back of the plane, containing a compressor, combustor, and turbine, that provides the plane with electricity and compressed air for the air conditioning system while the plane is on the ground.” The APU also provides the first step in starting the jet’s main engines and causing its blades to rotate at the tens of thousands of RPMs necessary for the engine to become sufficiently self-sustaining and propel the plane through liftoff and flight.
Only after passengers are buckled in and their tray tables are upright and secured does the APU begin sending compressed air to the jet’s main gas turbine engines. The compressed air passes through a small turbine on the outside of the engine, causing it to spin. Attached to the turbine is a shaft which is joined by gears to the main engine shaft, and that begins spinning as well.
“The blades connected to the engine shaft then start rotating faster and faster,” explains Brand. “The part you can see in the front of the engine is the fan, which is a big compressor that provides a lot of the thrust that moves the plane,” explains Brand. “There’s also a smaller, more powerful compressor behind the fan inside the engine that raises the pressure and the temperature of the air, preparing it for combustion with jet fuel.” Once the blades are moving fast enough, the pilot slowly adds fuel into the combustor section of the engine. There, an electric spark ignites the air and fuel mixture, and the exhaust passes from the combustor out through a turbine consisting of still more blades, speeding up the engine until it reaches idle, the point at which it is self-sustaining. Thrust is produced when the pilot adds more fuel, which speeds up the engine even more, increasing its power output.
This arrangement of meshing gears, spinning shafts, and rotating blades might seem pretty complicated, but the process is as basic as Newton’s third law of physics: For every action, there is an equal and opposite reaction. As the compressed air and fuel mixture is ignited in the engine’s combustion chamber, gases form and expand, exerting force and providing forward thrust as they shoot from the rear of the engine, causing the aircraft to move forward.
“Most commercial aircraft have used this engine-starting method for a long time,” says Brand. “The compressed air is already being produced by the APU, so there’s very little redundancy in the system.”
Thanks to Murtaza of Bangalore for this question.
Posted: March 19, 2013